Diecasting is a complex manufacturing technique that plays a vital role in creating intricate metal parts with accuracy and precision. The process involves introducing liquid metal into a cavity with high pressure which allows for the production of exquisite shapes and intricate designs that are difficult for other processes. Diecasting is widely used across various industries, including electronic, aerospace, automotive and even consumer products because of its high efficiency and ability to produce quality parts. This article explains the intricacies of diecasting, discussing its techniques, benefits in use, and the application.

Diecasting starts with the making of premium steel molds, also referred to dies. These molds are created to stand up to the extreme pressures and temperature of the molten metal. Dies are carefully designed to take in intricate details and maintain tight tolerances, making sure that every part cast meets specific design requirements. In the process of casting, metals such as aluminum, magnesium, zinc, as well as copper are first melted before being in the cavity of the die with high pressures. Rapid injections and cooling result in parts that have high dimensional stability and a smooth surface. The high precision of dies permits the production of parts with intricate geometries, which are often unattainable by other methods of manufacturing.
One of the major benefits of diecasting is its capacity to make parts with amazing dimensional precision as well as smooth surface finishes. This is because high-pressure injection makes sure that every detail in the mold is recreated, resulting in parts which meet the strictest tolerances and require minimal to any post-production effort. This is especially beneficial in the creation of complex geometries as well as fine details that might be difficult or impossible to achieve with other manufacturing techniques. Additionally, the repeatability of diecasting makes it ideal for production on a large scale, as it ensures that the exactness of thousands of pieces. The efficiency of the process is also a major source of costs savings as it decreases waste material as well as labor expenses.
Diecasting is widely employed across many industries due to its versatility as well as the variety of different materials used. For the automotive sector Diecasting is a must to make components like engines, transmission cases as well as structural components. The aerospace industry has a dependence upon diecasting for light, high-strength parts that can withstand the demanding conditions of flying. In electronics for consumers, diecasting components are employed for frames and housings that offer the durability and accuracy required in electronic devices. Diecasting's flexibility is evident in applications such as the communications, medical, as well as power tools industry showing its extensive use and significance. To get more details please head to Senadiecasting
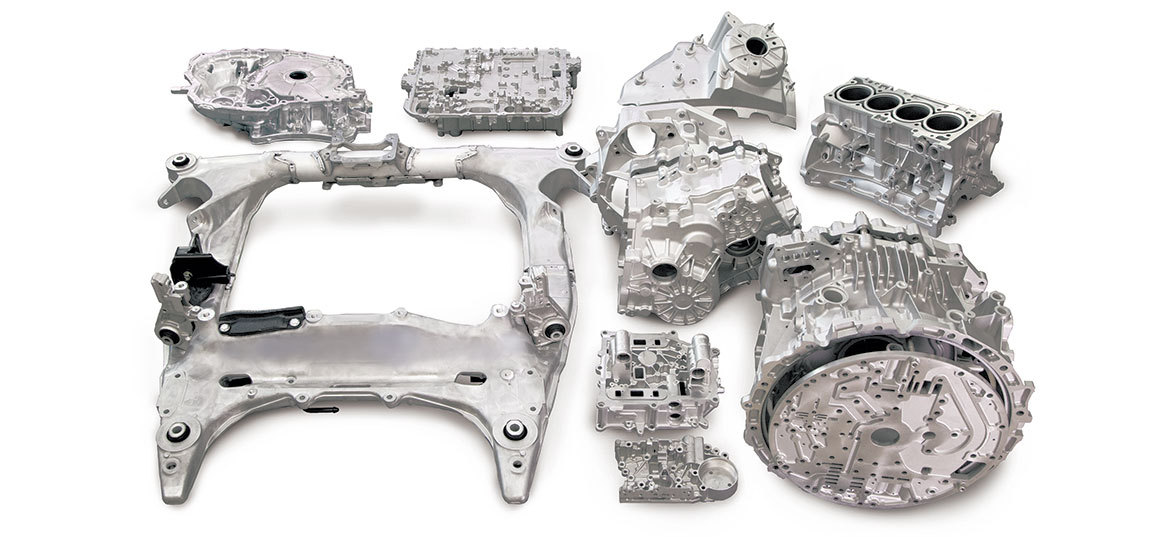
The diecasting material used can play an important role in determining the physical properties and functionality of the finished product. Aluminum is one of the most commonly used materials due to its high strength-to-weight ratio, corrosion resistance, along with its high electrical and thermal conductivity. Zinc alloys are also very popular for their strength, ductility, and the capacity to make components with fine specifics. Magnesium alloys benefit from the advantages of being the lightest structure metal. They are ideal for applications that require weight reduction. Copper alloys, although somewhat less popular, are used due to their high electro-conductive properties and corrosion resistance. The material selection depends upon the specifications of the project, which includes the mechanical properties, environment conditions and price aspects.
Diecasting is a zenith of manufacturing technology, offering a blend of precision, efficiency, and versatility that's unmatched by other manufacturing processes. Its ability to make complex, high-quality components with outstanding mechanical properties make it indispensable in many sectors ranging from automotive to consumer electronics. The efficiency and material savings inherent in the diecasting process highlight its importance in large-scale manufacturing, and its flexibility guarantees that it is able to accommodate the changing demands of modern manufacturing. As companies continue pushing the limits of technology and productivity, diecasting is expected to remain a critical tool, making advancements possible and supporting the creation of innovative products that are shaping our lives.